La risposta ricorrente é: "I giri li senti...mentre lavori"
In parte è vero, la sensibilità e “l’orecchio” dell’operatore sono fondamentali per ottimizzare i “giri” della fresa.
Tuttavia esistono delle regole basilari per migliorare sia il rendimento di taglio dell’utensile che la qualità delle superfici lavorate.
È infatti di abitudine parlare sempre e solo di numero di giri della fresa ma in verità dovremmo parlare di velocità di taglio della fresa e cioè della velocità relativa al tagliente determinata dal numero di giri della fresa moltiplicato per la lunghezza della sua circonferenza .
È evidente quindi che per mantenere invariate le condizioni di taglio, in base al diametro della fresa dovremo variare il numero di giri nel seguente modo:
- al diminuire del diametro della fresa aumentare i giri
- all’aumentare del diametro della fresa diminuire i giri
La formula semplificata per stabilire il numero di giri è la seguente:
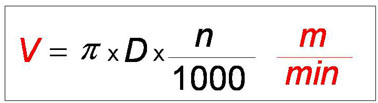
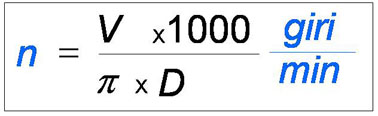
Considerando ottimali velocità di taglio con valori compresi tra 20 e 50 m/min:
VELOCITÀ 20 VELOCITÀ 50
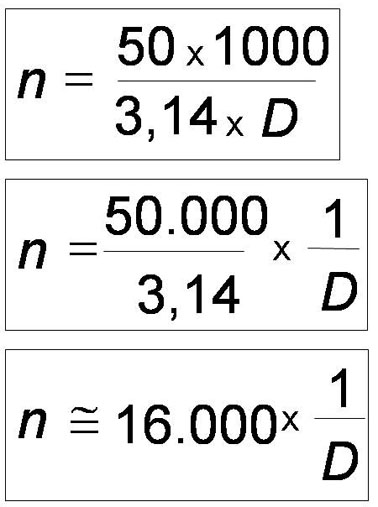
il numero di giri consigliato può variare da circa 6.400 a 16.000 giri/min per le frese di diametro 1 mm.
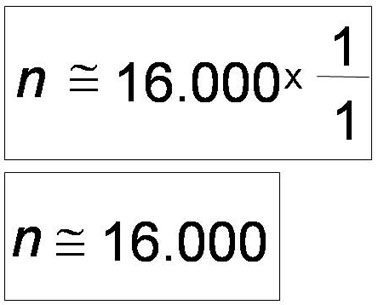
Se la fresa ha un diametro maggiore (es. d= 2mm) il numero di giri consigliato va diviso per il diametro stesso, cioè 2, e quindi può variare da 6400/2 = 3300 a 16000/2 = 8000 giri/min .
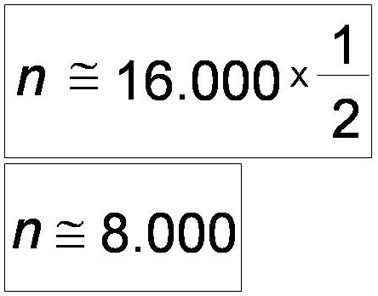
Se la fresa è conica?
Dato che il diametro della fresa conica varia al variare della posizione del tagliente si prende come riferimento il diametro di punta, solitamente 1,5 mm, e si somma 0,1 mm di diametro per ogni grado di inclinazione della fresa.
Se la fresa ha un'inclinazione di 2° il diametro di riferimento sarà 0,1x2= 0,2+1,5=1,7 mm
Se la fresa ha un'inclinazione di 4° il diametro di riferimento sarà 0,1x4= 0,4+1,5=1,9 mm
Se la fresa ha un'inclinazione di 6° il diametro di riferimento sarà 0,1x6= 0,6+1,5=2,1 mm
Se cambio materiale devo variare il numero di giri?
Anche il tipo di materiale lavorato può influire sul calcolo della velocità di taglio utilizzando indicativamente il seguente criterio:
- materiali facilmente lavorabili, aumentare il numero di giri (max velocità 50 m/min cioè 16.000/d)
- materiali più duri o più teneri diminuire il numero di giri (min velocità 20 m/min cioè 6.400/d) .
Se cambio tipo di fresa devo variare il numero di giri?
Anche il tipo di tagliente della fresa può determinare una variazione della velocità di taglio:
- frese a taglio medio: aumentare il numero di giri (max velocità 40 m/min cioè 12.000/d)
- frese a taglio fine o grosso: diminuire il numero di giri (min velocità 20 m/min cioè 6.400/d) .
Il tipo di macchina utilizzata può influenzare la scelta del numero di giri?
Anche il tipo di isoparallelometro utilizzato può influenzare la regolazione della velocità di taglio.
Macchine più rigide e performanti consentono di utilizzare un numero di giri più elevato e quindi ridurre i tempi di lavorazione.
Comunque è sempre consigliabile saggiare il “mordente” della fresa portandola a contatto del lavoro e, variando il numero di giri, valutare le vibrazioni (devono essere le minori possibili) ed il suono emesso (non dev’essere né cupo né stridulo).
E Il raffreddamento e/o la lubrificazione della fresa può influenzare la scelta del numero di giri?
Nelle lavorazioni manuali (non automatiche) la presenza di un sistema di raffreddamento/lubrificazione non comporta variazioni sensibili della velocità di taglio.
I vantaggi tangibili dati dall’utilizzo di questi sistemi, si riscontrano con la maggior durata e pulizia degli utensili e dalla rugosità e lucentezza delle superfici lavorate.
Che forza va esercitata sulla fresa durante la lavorazione?
É difficile quantificare la forza che l’operatore applica al mandrino dell’isoparallelometro durante la lavorazione.
Ovviamente “carico leggero” durante la finitura, “carico pesante” durante le fasi di sgrossatura in un campo di valori compreso tra 0,2 N e 2 N (20g e 200g).
É possibile con le frese da sgrossatura di diametro >= 2 mm aumentare la forza di lavoro fino a 4 N (400 g), impiegando isoparallelometri strutturalmente adeguati per sopportare le maggiori sollecitazioni.
Per valutare la forza di lavoro consigliamo di allenare la mano di presa afferrando come se fosse l’impugnatura della macchina un oggetto di diametro pressappoco equivalente e del peso di circa 1N (100 g).
Seduti sul posto di lavoro dinanzi alla macchina con l’avanbraccio rivolto verso l’alto (come se la macchina non fosse appoggiata sul banco ma sulla parete) simulare il movimento di fresaggio (su, giù, avanti, indietro, destra, sinistra) per almeno una ventina di secondi. Quindi afferrare l’impugnatura della macchina e fresare.
Come si fa ad ottenere una superficie fresata “precisa e perfetta”?
Rammentiamo che una superficie precisa non deve essere necessariamente “a specchio” anche se l’aspetto lucido fa sempre un “gran bell’effetto” e suscita un’impressione di accuratezza.
La precisione della superficie fresata è condizionata da i seguenti fattori che incidono direttamente sui rispettivi elementi :
A) L’isoparallelometro ed in particolare il suo livello di precisione che regolano il parallelismo tra le pareti fresate;
B) Il metallo utilizzato che influenza la specularità della parete fresata e la durata dell’utensile utilizzato;
C) Il grado di precisione della fresa utilizzata che determina la linearità e la rugosità della parete fresata;
D) La manualità ed esperienza dell’operatore che incide sempre sulla qualità del lavoro ma diventa fondamentale qualora i tre
fattori precedenti non siano in possesso dei requisiti essenziali.
Vuoi saperne di più?
Forse potrebbe interessarti anche: